Der Ventilatormotor
- Reinigung
- Lager ersetzen
- Kollektor überdrehen
- Auswuchten
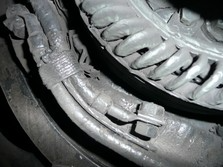
Feld Ankerwicklung

13302 Typenschild Ventilatormotor
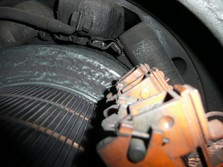
13302 Kollektor Wicklung
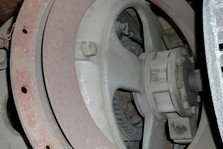
13302 Lager Seite Rad
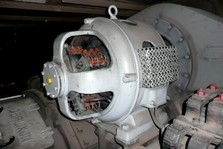
13302 Lager
Nach der gründlichen Reinigung erfolgte eine erste Widerstandsmessung, die enttäuschend ausfiel. Mittels eines Spezialverfahrens wurde der Motor nochmals gereinigt und getrocknet, die Werte wurden aber leider nicht besser. Ein Vergleich mit solchen Motoren, die bei der BLS im Einsatz sind ergab, dass weder bei den Feld- noch bei den Ankerwicklungen die minimalen Widerstandswerte erreicht wurden. Somit war unser Ziel nur noch mit einer Neu –Wicklung zu erreichen. Es wurde noch diskutiert, ob doch der in Betrieb stehende Motor ausgebaut und revidiert werden sollte. Da kaum viel bessere Werte zu erwarten waren und mit der Demontage und Reinigung des Reserve-Motors die Risiken nun bekannt waren, wurde diese Variante fallen gelassen. Ausserdem waren mit den bisherigen Arbeiten bereits erhebliche Kosten angefallen.
Nun liessen wir von 3 Firmen eine Offerte erstellen. Die Kosten bewegten sich nun plötzlich zwischen 20'000 und 27'000 Franken statt der budgetierten 2'500 Franken.
Nach verschiedenen Gesprächen konnten wir uns mit der Firma, die den Motor bereits demontiert und ausgemessen hatte, auf einen Festpreis von Fr. 22'050 festlegen. Dieser beinhaltete auch die bereits geleisteten Arbeiten sowie die MWST. Der hohe Preis resultierte aus dem hohen Materialaufwand (Kupfer etc.), weil der Motor mit der Bahn-Frequenz von 16,7 Hertz betrieben wird. Ausserdem gibt es nur noch wenige Firmen, die sich eines solchen Museumsstückes annehmen. Auch dies ist also eine Technik, bei der das Fachwissen immer mehr verloren geht!
Für Interessierte: Die Motordaten sind aus dem Typenschild ersichtlich.
Der Preis von Fr. 22'050 Fr. ist fast das 9fache des ursprünglich budgetierten Betrages. Dazu kommt dann noch der Motorentausch bei der SOB. Dies alles belastet die Krokodilkasse stark. Als Gegenwert erhalten wir einen neuwertigen Motor, der das Krokodil überleben dürfte.

Die Zugsicherung
Ort: Ausfahrt Ziegelbrücke
Neue Lagerschalen
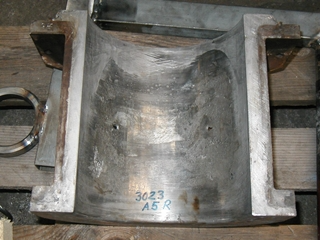

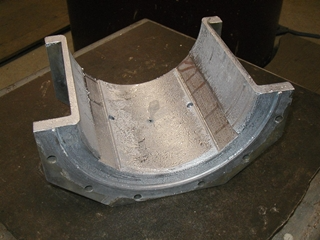
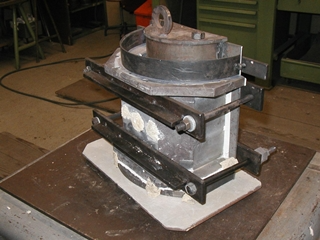
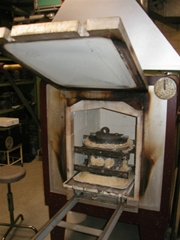

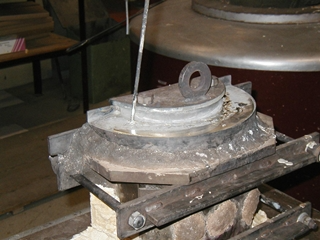

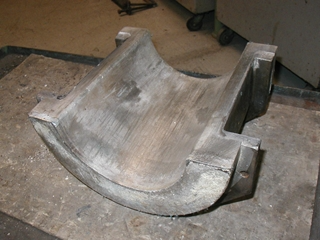


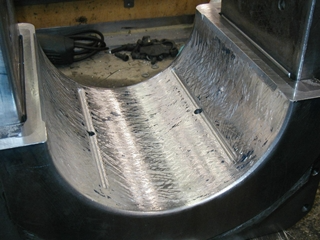
Aus alt wird neu
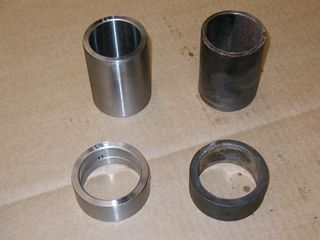

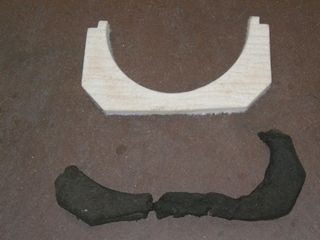
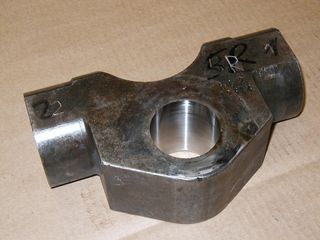
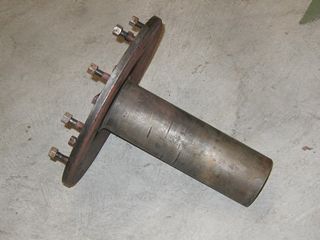

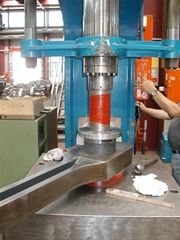
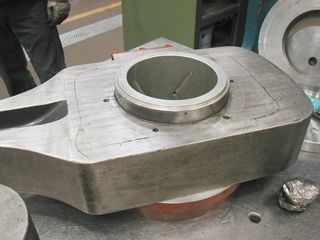
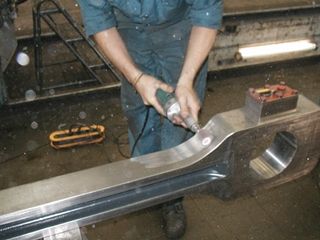

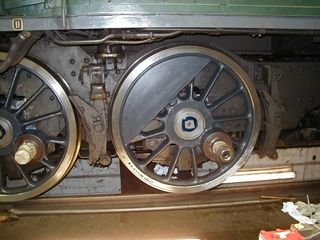
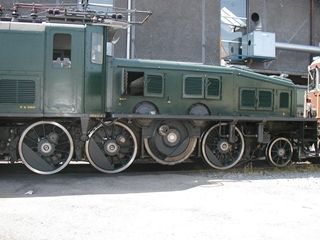
Die Lokomotive ist fast bereit für die Montage der aufgearbeiteten Kuppelstangen.
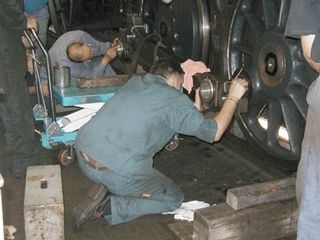
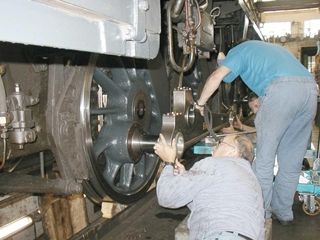
